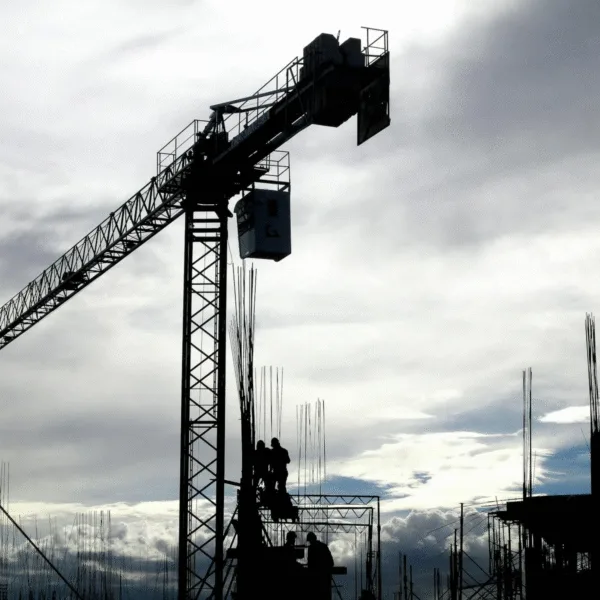
Introduction
When operating heavy machinery, the crane joystick serves as your primary interface for precision control. Choosing the right industrial crane joystick can dramatically impact productivity, safety, and equipment longevity. This guide reveals the 7 critical features that define high-performance crane joysticks for demanding applications.
1. Rugged Industrial-Grade Construction
A quality crane joystick must withstand harsh environments. Look for:
- IP67 or higher waterproof rating
- Reinforced metal housing
- Shock-resistant components
- Corrosion-proof materials
Premium crane joysticks use aircraft-grade aluminum alloys that survive extreme temperatures (-30°C to +70°C) and resist chemical exposure.
2. Precision Control with High Resolution
Advanced crane joysticks feature:
- 16-bit resolution for smooth operation
- 0.1° control accuracy
- Adjustable sensitivity settings
- Zero dead-zone design
This ensures millimeter-perfect positioning of heavy loads, reducing operator fatigue and improving safety.
3. Ergonomic Operator Comfort
Top-tier crane joysticks prioritize user experience with:
- Contoured handgrips with anti-slip coating
- Adjustable palm rests
4. Advanced Safety Features
Critical safety elements in professional crane joysticks include:
- Emergency stop button
- Fail-safe position return
- Overload protection
- Redundant signal verification
These features prevent accidents and comply with ISO 13849 safety standards.
5. Multi-Function Control Options
Modern crane joysticks offer versatile configurations:
- 2-axis to 8-axis control
- Integrated thumb wheels
- Programmable buttons
- CAN bus/J1939 compatibility
This flexibility allows customization for specific crane models and applications.
6. Long Service Life with Minimal Maintenance
Durable crane joysticks feature:
- Self-lubricating bearings
- Sealed contactless sensors
- Replaceable wear components
- 10+ million operation cycles
High-quality models offer MTBF (Mean Time Between Failures) exceeding 50,000 hours.
7. Smart Connectivity and Diagnostics
Next-generation crane joysticks include:
- Bluetooth configuration
- Real-time performance monitoring
- Predictive maintenance alerts
- Firmware update capability
These IoT features enable proactive maintenance and reduce downtime.
Conclusion
Selecting the optimal crane joystick requires careful evaluation of these 7 critical features. Premium crane joysticks combine rugged construction, precision control, and smart technology to deliver superior performance in the most demanding industrial environments. By prioritizing these characteristics, operators can achieve safer, more efficient crane operations with reduced maintenance costs.
Introduction to Industrial Control Interfaces
In the realm of heavy machinery operation, the control interface serves as the crucial connection between operator and equipment. For professionals working with overhead cranes, gantry systems, and other lifting apparatus, selecting the appropriate control mechanism requires careful consideration of multiple technical and ergonomic factors. This in-depth examination explores seven fundamental characteristics that distinguish superior control devices in demanding industrial environments.
1. Robust Mechanical Construction for Industrial Environments
The physical durability of control interfaces cannot be overstated in industrial settings. Superior models feature:
- Military-grade aluminum or stainless steel housing that resists impact damage
- Environmental sealing that meets or exceeds IP67 standards for dust and water resistance
- Specialized coatings that prevent corrosion from chemicals, salt spray, or humidity
- Internal components rated for operation in extreme temperature ranges (-40°C to +85°C)
Manufacturers often subject these components to accelerated life testing, simulating years of continuous use in harsh conditions. The best control interfaces can withstand direct exposure to hydraulic fluids, lubricants, and cleaning solvents without degradation of performance.
2. Precision Engineering for Accurate Load Positioning
Modern lifting operations demand millimeter-level accuracy in load placement. High-end control interfaces achieve this through:
- High-resolution optical or magnetic position sensors with 14-16 bit resolution
- Advanced signal processing that eliminates mechanical dead zones
- Programmable response curves that can be customized for different load weights
- Dual-channel signal verification that prevents erroneous inputs
The precision components in these systems often feature aerospace-grade bearings and contactless sensing technology that maintains accuracy through years of continuous operation. Many models include automatic calibration routines that compensate for normal wear over time.
3. Ergonomic Design for Operator Comfort and Safety
Operator fatigue represents a significant safety concern in material handling operations. Leading manufacturers address this through:
- Anthropometrically designed grips that accommodate various hand sizes
- Adjustable resistance mechanisms that allow customization of control feel
- Vibration damping systems that reduce hand-arm vibration syndrome risks
- Thermally insulated surfaces that remain comfortable in extreme temperatures
Clinical studies have shown that properly designed control interfaces can reduce operator fatigue by up to 40% during extended shifts. Many models now incorporate biometric sensors that can alert supervisors when operator fatigue reaches concerning levels.
4. Comprehensive Safety Systems Integration
Industrial control interfaces incorporate multiple layers of safety features:
- Dual-circuit emergency stop mechanisms with positive break contacts
- Automatic load moment indication that prevents dangerous overload conditions
- Redundant position sensing that cross-checks input validity
- Programmable safe zones that limit operational parameters
These safety systems typically comply with international standards including ISO 13849 (Performance Level e) and IEC 62061. Advanced models feature self-diagnostic routines that continuously monitor system integrity and can predict potential failures before they occur.
5. Versatile Control Configurations
Modern industrial operations require flexible control solutions:
- Modular designs that support single-axis to eight-axis configurations
- Integrated auxiliary controls for functions like tool rotation or grapple operation
- Field-programmable button assignments that adapt to different workflows
- Multiple protocol support (CANopen, J1939, Profibus, Ethernet/IP)
This flexibility allows the same control interface to be used across different equipment types, reducing training requirements and inventory complexity. Many models support configuration profiles that can be quickly switched between different operational modes.
6. Maintenance-Friendly Design Features
Industrial components must balance durability with serviceability:
- Modular construction that allows component-level replacement
- Tool-less access to frequently serviced components
- Standardized replacement parts across product families
- Clear diagnostic indicators for quick troubleshooting
Leading manufacturers provide detailed maintenance interval recommendations based on actual usage data from field monitoring. Some advanced models incorporate usage tracking that automatically alerts maintenance teams when service is due based on actual operating conditions rather than calendar time.
7. Smart Connectivity and Data Integration
The Industrial Internet of Things (IIoT) has transformed equipment monitoring:
- Built-in data logging of operational parameters
- Wireless firmware updates that eliminate downtime for upgrades
- Cloud-based performance analytics that identify usage patterns
- Integration with enterprise asset management systems
These smart features enable predictive maintenance strategies that can reduce unplanned downtime by up to 30%. The data collected from control interfaces often provides valuable insights into operator behavior and equipment utilization patterns that can inform broader operational improvements.
Conclusion: Selecting the Optimal Control Solution
Choosing the right control interface for industrial lifting equipment requires careful evaluation of multiple technical and operational factors. The seven characteristics outlined in this guide represent the current state of the art in control interface technology. By prioritizing these features, equipment operators and maintenance professionals can ensure reliable performance, enhanced safety, and reduced total cost of ownership. As control technology continues to evolve, we can expect even greater integration with digital systems and more advanced predictive capabilities in future generations of industrial control interfaces.